OPC Clinker, or Ordinary Portland Cement Clinker, is the key ingredient used in the production of Ordinary Portland Cement, one of the most commonly used types of cement globally. This clinker is formed by heating limestone and clay materials in a kiln to a sintering temperature, which is typically around 1450°C. The chemical process involves the formation of nodules, or clinker, from calcium carbonate, silicon, aluminum, and iron oxides.
Composition and Production
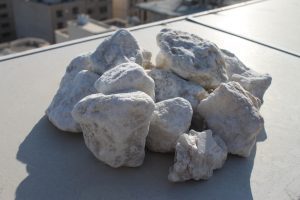
OPC Clinker
Raw Materials: The primary materials used in OPC clinker production include limestone (calcium carbonate) and clay or shale (silicon, aluminum, and iron compounds). These materials are finely ground and mixed in precise proportions.
Kiln Process: The mixture is fed into a rotary kiln where it undergoes a series of chemical reactions. The intense heat causes the raw materials to react and form new compounds, primarily tricalcium silicate (C3S) and dicalcium silicate (C2S), which are crucial for cement’s hydraulic properties.
Cooling: After exiting the kiln, the hot clinker is rapidly cooled in a cooler to stabilize the compounds and preserve the desired mineral structure.
Properties
Hydraulicity: OPC clinker has strong hydraulic properties, meaning it hardens when mixed with water due to the hydration reactions of its compounds, primarily C3S and C2S.
Strength: The strength of cement produced from OPC clinker is primarily determined by the proportion of C3S, which contributes to early strength, and C2S, which contributes to long-term strength.
Fineness: The fineness of ground clinker (cement) affects the rate of hydration and the development of strength.
Applications
Construction: OPC is used in a wide range of construction projects, including residential, commercial, and infrastructure development due to its versatility and strength.
Concrete Production: OPC clinker is a key ingredient in concrete, which is used for foundations, structural components, and pavements.
Mortar and Plaster: It is also used in the preparation of mortar for masonry work and plaster for finishing surfaces.
Environmental Impact
Carbon Emissions: The production of OPC clinker is energy-intensive and results in significant CO2 emissions. Efforts are being made to reduce the carbon footprint through alternative materials and more efficient processes.
Sustainability: The industry is exploring the use of supplementary cementitious materials (SCMs) like fly ash and slag to reduce clinker content in cement, enhancing sustainability.
Innovations and Trends
Alternative Fuels: The use of alternative fuels in kilns is increasing, which helps reduce reliance on fossil fuels and lowers emissions.
Green Cement: Research is ongoing into the development of greener cements that replace part of the clinker with alternative materials, reducing overall environmental impact.