Understanding the Key Factors Affecting Cement Prices
Cement, a crucial material in construction, is subject to a variety of economic forces that influence its price. Understanding these factors helps in predicting market trends and managing costs in construction projects.
Raw Material Costs: The foundation of cement manufacturing lies in key raw materials like limestone, clay, and iron ore. These materials are essential in the production process, and any fluctuation in their prices directly affects the overall cost of cement. For instance, if the cost of limestone rises due to increased mining expenses or supply shortages, the production expenses inevitably climb, leading to higher prices for the mentioned material. Additionally, the fuel required to process these raw materials plays a significant role in determining the final cost.
Energy Expenses: Energy is a major component in the production of cement, with fuel being particularly critical. The production process requires significant amounts of heat, typically generated from coal, natural gas, or oil. As energy prices fluctuate, so do the production costs. When fuel prices rise, manufacturers face higher production expenses, which are often passed on to consumers through increased cement prices. Conversely, when energy costs drop, there may be a decrease in cement prices, assuming other factors remain constant.
Transportation Costs: Another critical factor is the cost of transporting concrete binder from production plants to construction sites or markets. Cement is a heavy material, and transporting it over long distances can be expensive. Rising fuel prices can increase these transportation costs, subsequently impacting the final price of cement. Moreover, infrastructure issues, such as poorly maintained roads, can lead to higher transportation expenses, further affecting prices.
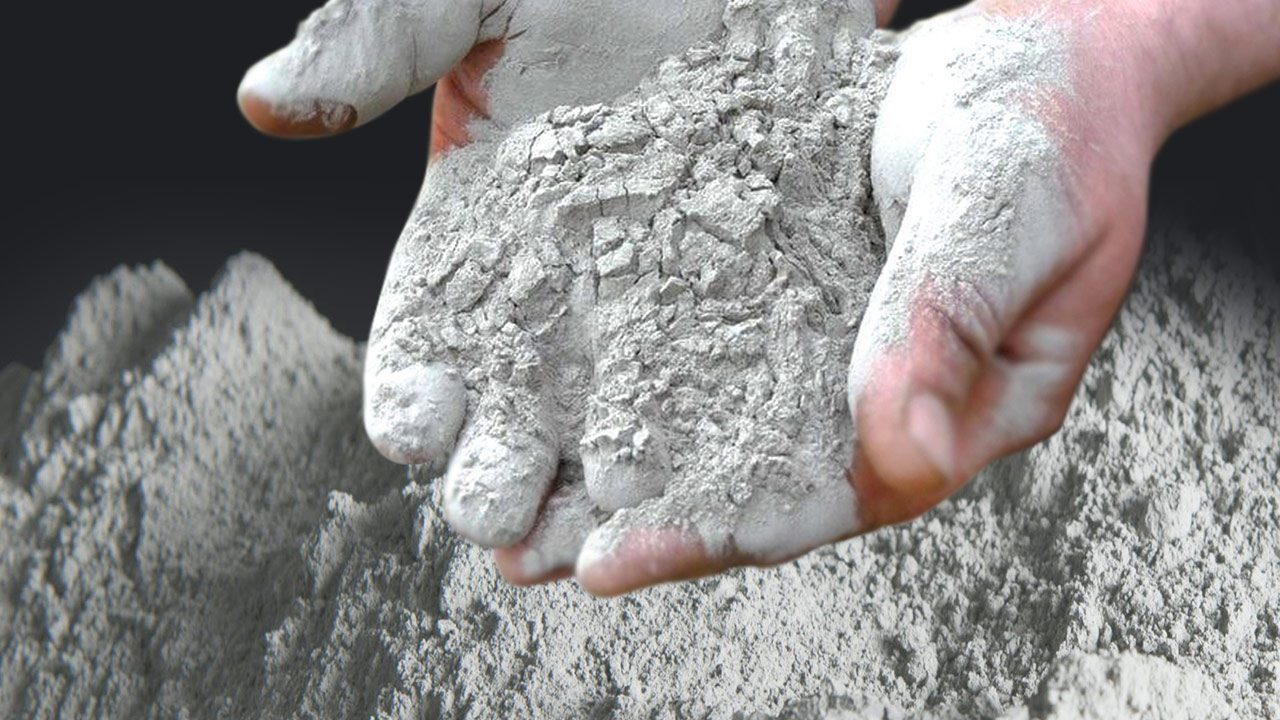
Currency Exchange Rates: In a globalized market, currency exchange rates can significantly impact grout prices. If the local currency weakens against the currency in which cement or its raw materials are traded, the cost of importing these materials increases. This, in turn, raises production costs and ultimately the price of cement. Currency fluctuations are particularly influential in countries that rely heavily on imported raw materials or energy.
Government Regulations: Governments play a crucial role in regulating industries, and the cement sector is no exception. Environmental controls, taxes, and new regulations can increase production costs. For instance, stricter environmental laws may require companies to invest in cleaner technologies, which can be expensive. These additional costs are often reflected in the price of cement.
Supply and Demand Dynamics: The balance between supply and demand is a fundamental economic principle that affects all commodities, including cement. When demand for mortar binder is high, but supply is limited, prices tend to rise. Conversely, if there is an oversupply and demand is low, prices may decrease. This dynamic is influenced by various factors, including economic growth, construction trends, and even natural disasters that can disrupt supply chains.
Technological Advancements: Innovation in cement production can lead to more efficient manufacturing processes, reducing costs. Technological advancements that allow for quicker, less energy-intensive production can lower expenses and potentially lead to a decrease in prices. However, these savings may be offset by other rising costs, such as raw materials or transportation.
Political Stability and Labor Costs: Political stability is crucial for the smooth operation of cement production and distribution. In regions where political unrest is common, supply chains can be disrupted, leading to shortages and price hikes. Additionally, labor costs, including wages and benefits, also influence concrete binder prices. Increases in labor expenses raise production costs, which can lead to higher prices for consumers.
Conclusion: Cement prices are influenced by a complex interplay of factors, from raw material costs to political stability. By understanding these dynamics, stakeholders in the construction industry can better anticipate price changes and make informed decisions.